Power Plant Safety Gets a Boost - Human Fatalities Prevented
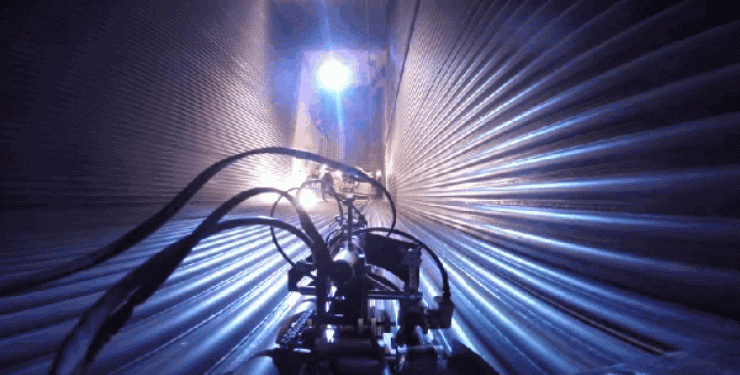
In the cinematic world, legions of robots capable of scaling walls is usually a cause for concern for the film’s protagonist. In the real world however, robots are being programmed to perform such feats in order to takeover some of society’s most dangerous or unpleasant jobs, not only saving lives in the process, but also saving companies in the energy sector thousands, if not millions of dollars.
While the future of robotics has yet to be written, it will likely encompass many awe-inspiring applications, of which most can hardly even be imagined. That being said, the inclusion of robots in nearly any contemporary process is bound to make it less time consuming, more efficient, and safer for all those involved.
Robotics and Infrastructure Integrity
To inspect the integrity of a power plant’s boilers, an undertaking so complex and costly that it is typically only done about once a year, human technicians would have to erect scaffolding upwards of 150 feet in height, spend days scouring over every square inch of the boiler’s surface, in dirty, less than ideal conditions.
Approximately 20 to 30 technicians suffer a serious injury or lose their lives each year due to a fall while inspecting the many plants that power North America. Like many applications for which robotic technology is being developed, the fundamental need to improve the working conditions for these technicians is what’s driving the development of these robots, which are designed to travel along a pre-installed framework.
Conventional plant inspections are also spectacularly costly – it’s estimated that for every day a plant is shut down for inspections, nearly a million dollars in revenue is lost. Currently, the average human driven inspection can take upwards of seven days to complete. All told, the power plant inspection business is currently worth about $17 billion dollars annually, a cost that is not surprisingly passed on to the consumer.
A start up technology firm called Gecko Robotics is looking to change all that thanks to their wall crawling robots. Using ultrasonic technology, a deployed fleet of robots can inspect and analyze infrastructure integrity in about a day, all while keeping the operators safe. Since the data is collected using sound waves, more complete information can be gathered over a traditional visual inspection. Financially speaking, robotic inspections can save energy companies hundreds of thousands each and every year.
The potential of this technology is far from being limited to power plants however, and can be applied anywhere infrastructure inspection is deemed too dangerous to be performed by human workers. For instance, bridge, subway, skyscraper, and other infrastructure inspectors, could all equally benefit from this technology.
Though the technology hasn’t been widely adopted yet, it’s difficult to come up with a reason it won’t be (saving lives and reducing costs tend to act as enough of a motivator when paired together). As such, it’s safe to assume that the number of support staff to service and maintain these robots will experience commensurate growth with the adoption of the robotic technology itself, leading to thousands of new jobs in the electronic technician and electromechanical technician fields. These courses, both offered at George Brown College, provide a comprehensive introduction to electronic and electromechanical systems that are essential for students looking to make their mark in a burgeoning industry.
Many might claim that it’s just a matter of time before the manufacturing sector is almost completely autonomous - and while it might be easy to see why that thought might initially cause human workers to fear for their jobs, it’s equally easy to wonder at the incredible opportunities that are beginning to make themselves known in the world of robotics.