3 Disruptive Technologies That are Transforming Manufacturing
The world of manufacturing is drastically changing. New technologies are leading to what analysts describe as the fourth industrial revolution, otherwise known as Industry 4.0, a term that was introduced at the Hannover Fair in 2012 by German workers. The fourth industrial revolution is marked by the introduction of disruptive technologies, where machines and robots can make decisions and perform tasks on their own without human intervention in an autonomous system.
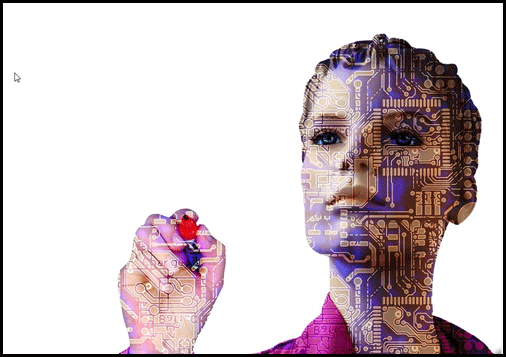
Below are three disruptive technologies that are revolutionizing the manufacturing industry:
1. AI and Smart Robots
Industrial robots are most commonly used to carry out repetitive tasks with common applications such as materials handling or robotic welding. However, in this new manufacturing era, robots are becoming more advanced and adaptive, and can even solve problems like humans.
Today’s robots are designed with greater computing power, sensor technology to enable vision recognition, more sophisticated sound and movement detection, and tactile, force and torque control sensing. With advances in artificial intelligence (AI) software, robots can problem-solve in unstructured environments: a feature that’s much needed in a fast-paced industry with shorter products’ life cycle and a growing demand for customization.
Many of these robots are also being deployed to work on components that are too tiny for humans to efficiently manipulate, such as micro-electro-mechanical systems. While some robots are replacing human jobs, today’s robots such as smart robots are also designed to collaborate with humans. As well, human assistance from robotics technicians and factory workers are still needed to maintain the machines and provide support.
2. Internet of Things (IoT)
Internet of Things (IoT) is a fully connected and flexible system of interrelated computer devices, where intelligent devices communicate with each other without requiring human-to-human or human-to-computer interaction. In industrial settings, these devices are creating smart factories that are more flexible, efficient, and profitable. Through using constant stream of data from connected operations and production systems, it can learn and adapt to new demands.
The Internet of Things improve flexibility and responsiveness in manufacturing in the following ways:
Real-time data – Increase efficiency and responsiveness. This is especially important for industrial applications like quality control or employee safety which have real-time needs and requirements.
Better asset use – With access to more data than ever before, manufacturers can set goals, measure progress and constantly optimize their machines’ performance and product quality.
Predictive diagnostics – More data, delivered in real time, means manufacturers can locate, find and fix problems faster.
3. Virtual Reality (VR)
More than one-third of U.S manufacturers have already adopted VR systems. These systems generate a simulation of a 3D image or environment that can be interacted with in a seemingly real or physical way by a person using special electronic equipment.
Virtual reality in manufacturing give companies and manufacturers valuable foresight by allowing manufactures the ability to interact with VR designs in a realistic manner before actually building real-world designs. This can lead to more cost-effective products and a streamlined operation process.
Some companies, such as Ford and BAE, have adopted VR technology in their manufacturing process. Using the VR model, they can build models without designing a physical model to see how changes to the model or environment can affect it.
VR technology can also increase efficiency in the manufacturing process by stimulating production lines virtually, so production managers can see where bottlenecks would likely occur before any physical work is started. It can also increase safety by enabling technicians and management to identify potentially hazardous maneuvers early. Some other benefits of VR technology in manufacturing include providing visual cues for diagnoses, guiding workers, and making training more efficient.
Humans Are Still Needed In Industry 4.0
While disruptive technologies are becoming very advanced and can adapt to situations and make decisions on their own, humans are still needed to work alongside these machines. As well, because these technologies are very advanced, manufacturers require people who have high skill sets in order to operate and maintain these machines. Online industrial training courses makes it easy for students to gain the necessary skills and and knowledge for in-demand jobs. Learn more about our online courses in robotics.